Magnetic Materials Used in Puritan Permanent Type Separation Products
There are a couple of choices of magnetic materials to consider when choosing a magnetic separator; ceramic and rare earth.
Both of these are permanent magnets and will retain their full magnetic strength losing approximately ½ of 1% per 100 years if not subjected to physical abuse or temperatures that exceed their limitations.
Almost all magnetic separators are offered in either ceramic or rare earth. The application typically dictates which is the proper choice of materials.
The magnetic strength of the raw magnetic material is measured in megagauss oersteds (MGO). This number will change as the magnet is integrated into a piece of separation equipment.
By manipulating the north and south magnetic poles on the magnets thru placement and the use of steel pole pieces or back plates, the magnetic field is enhanced and directed into the
product flow area for optimum separation. These materials are brittle and cannot be used as a structural component in a design. The
actual magnetic material is secured within a stainless steel
enclosure.
Rare Earth Magnets
There are two types of rare earth magnets used in magnetic separators, Neodymium-Iron-Boron and Samarium Cobalt. Both are typically more expensive than ceramic, but provide a much higher MGO allowing for greater separation of ferrous fines. The term “rare earth” comes from the Neodymium and Samarium classification in the Lanthanides section of the Periodic Table of Elements.
Neodymium-Iron-Boron – This is the most commonly used rare earth material. The mills that produce this material are continually working on increasing the MGO. Until recently, the MGO for Neodymium-Iron-Boron used in separation magnets is between 45 and 50. We now offer the strongest available (52 MGO) Neodymium-Iron-Boron material! The range in strength is relative to the size and shape of the material being used due to limitations in the manufacturing process. The maximum working temperature is up to 300 degrees F.
Samarium Cobalt – This material is more expensive than the Neodymium-Iron-Boron and has a lower MGO value, between 24-28. However, Samarium Cobalt does offer higher working temperatures up to 575 degrees F.
- 10 times higher energy than ceramic, and can have 25 times the holding value
- Can handle high flow rates with optimum capture, especially on ferrous fines
- Delivers optimum separation performance for size, thus aIlowing reduction in magnet weight and size
- Puritan products utilize the highest grade magnetic materials available
- Available in Neodymium-lron-Boron and Samarium Cobalt
Composition and Manufacturing Process: Two types of rare earth materials are available. The first type Samarium Cobalt, consists of Samarium ,Cobalt, and Iron. The second and more commonly used is Neodymium. This is composed of Neodymium, Iron, and Boron.
The term "rare earth magnet" comes from Neodymium and Samariums classification in the lanthanides (rare earth) section of the periodic table of elements. The composite materials of these magnets are melted together and then milled into a powdered form.
This material is then dry pressed into the desired shape while a magnetic field is applied to orient the molecules. The final step includes sintering, being ground to the required dimension and magnetizing.
Alnico Magnets
Good magnetic reach out for capture of contaminants
Can be used effectively
up to 1000° F
Separation capabilities are similar to ceramic
Composition and Manufacturing Process: Two types of Alnico are available. One is cast and the other is sintered. Cast is poured in a molten form into a mold. Sintered is a powdered mixture that is dry pressed. Alnico consists of aluminum, nickel, cobalt, copper, iron, and sometimes titanium. While being cast or sintered sometimes a magnetic field is applied.
When subjected to the magnetic field this magnet is called anisotropic. When no magnetic field is applied this is called isotropic. After cooling, the magnets are ground to the desired dimension and magnetized.
Ceramic Magnets
The MGO of ceramic magnets is 3.50. This material offers low cost
and good protection. Ideal for plate type magnets to reach into deep product flows and extract ferrous contaminants. Will not be
as effective extracting ferrous fines as rare earth materials. Will withstand working temperatures of up to 850 degrees F.
- Offer good design flexibility in most separation applications
- Provide a strong, dense field for capture and control
- Holds their magnetic strength forever, resisting demagnetization
Composition and Manufacturing Process
Consists of a powdered mixture of barium or strontium and iron oxide which is put into a wet press or dry press for forming. While being pressed, a magnetic field is applied to orient the molecules and achieve the maximum performance potential.
Following the pressing process, the material is fired in a furnace to approximately 2000F. The final step requires the magnet to be finished ground to its desired size using a diamond grinding wheel then magnetizing.
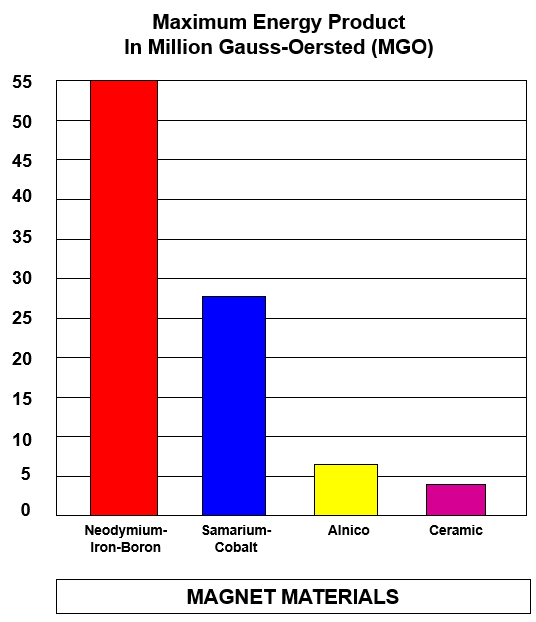
Other Features
Puritan magnetic designs resist demagnetization
Permanent magnetic design will not shut down during a power failure
Little or no maintenance, except for periodic cleaning
Note: Puritan magnets will retain their full magnetic strength unless subjected to extreme adverse conditions or
used improperly. Contact Puritan for detailed information.